4 Simple Techniques For Inventory Management
Wiki Article
A Biased View of Inventory Management
Table of ContentsSome Known Facts About Inventory Management.Inventory Management - The FactsSome Ideas on Inventory Management You Should KnowThe Only Guide for Inventory Management
There are two primary methods of monitoring inventory: periodic and continuous. The primary distinction between these is just how commonly data is upgraded. Regardless of how usually you track inventory, you may want to utilize one of the following supply management strategies: ABC Evaluation, ABC (Always Better Control) Analysis is inventory administration that separates various products right into 3 categories based upon pricing as well as is divided right into groups A, B, or C.The things in the B category are fairly cheaper compared to the A group. And the C category has the least expensive items of all 3. EOQ Version, Economic Order Quantity is a strategy utilized for planning and purchasing an order amount. It entails making a choice concerning the amount of inventory that must be placed in stock at any type of provided time. Inventory Management.
FSN Method, This method of supply control describes the procedure of maintaining track of all the things of inventory that are not made use of frequently or are not needed constantly. They are then categorized into three different groups: fast-moving inventory, slow-moving inventory, as well as non-moving stock. JIT Technique, Simply In Time inventory control is a process made use of by makers to manage their inventory levels.
:max_bytes(150000):strip_icc()/inventory-management-8595e839c2884128997ca77f00a8da2b.jpg)
How Inventory Management can Save You Time, Stress, and Money.
VED Evaluation, VED is a technique utilized by organizations to control their inventory. It primarily relates to the monitoring of crucial and preferable extra parts. The high level of stock that is needed for production typically warrants the reduced stock for those components. One of one of the most critical variables that a firm must think about is the precision of the details offered in its stock data sources.Wrike is a project administration option that can help you do exactly that. With Wrike's product administration tools, you can take care of every one of your item team's activities in one area and also obtain one of the most out of every project. Wrike's item launch automation helps increase product launches with a streamlined technique.
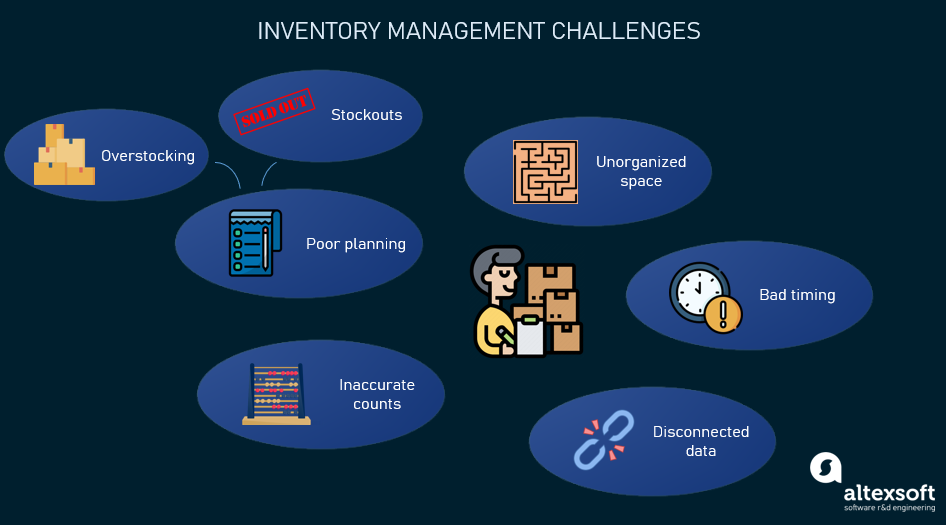
go to this site

Stock monitoring attempts to effectively enhance supplies to stay clear of both gluts and also lacks. 4 major stock management methods consist of just-in-time monitoring (JIT), products need preparation (MRP), economic order amount (EOQ), and days sales of supply (DSI).
A scarcity of stock when as well as where it's needed can be exceptionally destructive (Inventory Management). At the exact same time, stock can be considered a responsibility (if not in a bookkeeping sense). A big inventory brings the risk of putridity, burglary, damage, or shifts in need. Inventory should pop over here be insured, as well as if it is not offered in time it may need to be thrown away at clearance pricesor merely damaged.
Knowing when to restock stock, what amounts to purchase or produce, what price to payas well as when to market as well as at what pricecan easily become facility decisions. Local business will typically keep track of supply by hand and identify the reorder factors as well as amounts utilizing spreadsheet (Excel) formulas. Larger businesses will make use of customized business source preparation (ERP) software program.
Excitement About Inventory Management
Suitable inventory administration techniques differ depending on the market. An oil depot has the ability to store huge amounts of stock for extensive amount of times, permitting it to await demand to grab. While storing oil is expensive and riskya fire useful site in the U.K. in 2005 brought about millions of pounds in damages and also finesthere is no danger that the inventory will spoil or go out of style.For business with complicated supply chains and manufacturing procedures, stabilizing the risks of inventory excess as well as scarcities is specifically difficult. To accomplish these balances, companies have established numerous techniques for stock administration, including just-in-time (JIT) as well as materials demand preparation (MRP). Some business, such as economic solutions companies, do not have physical inventory therefore has to rely upon service procedure administration.
Stock has to be literally counted or measured prior to it can be placed on an annual report. Companies typically keep sophisticated supply management systems qualified of tracking real-time stock degrees. Supply is accounted for making use of among 3 methods: first-in-first-out (FIFO) setting you back; last-in-first-out (LIFO) setting you back; or weighted-average costing. An inventory account usually contains 4 different categories: Resources represent numerous products a business purchases for its production procedure.
Work in procedure (additionally referred to as goods-in-process) represents basic materials in the process of being changed into a finished item. Completed items are completed items easily offered available for sale to a firm's clients. Goods stands for finished products a company gets from a vendor for future resale. Depending on the kind of company or item being assessed, a business will certainly use different supply management techniques.
Report this wiki page